Enhance Your Prints With Top-notch Printing Ink Quality Control – Click To Optimize Your Results!
Printing Ink Quality Control: Ensuring Excellence in Print
Introduction
Dear Readers,
3 Picture Gallery: Enhance Your Prints With Top-notch Printing Ink Quality Control – Click To Optimize Your Results!
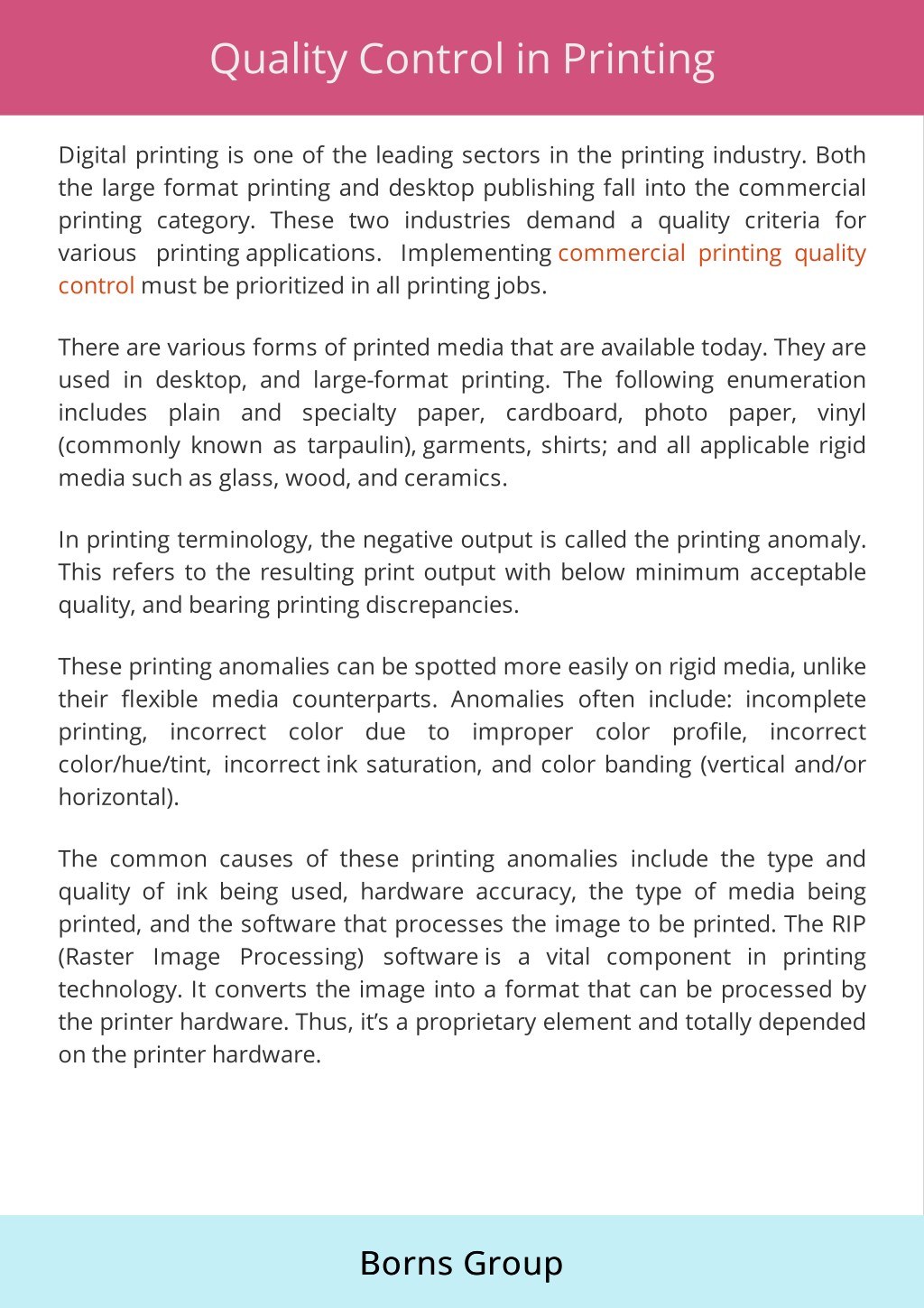
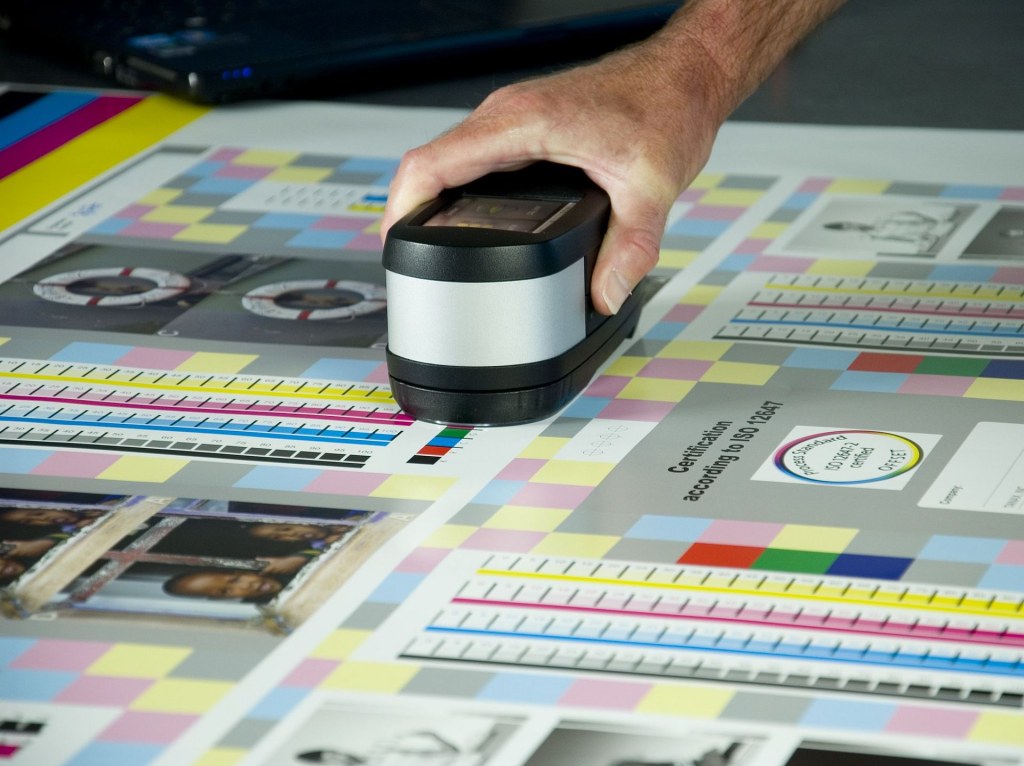
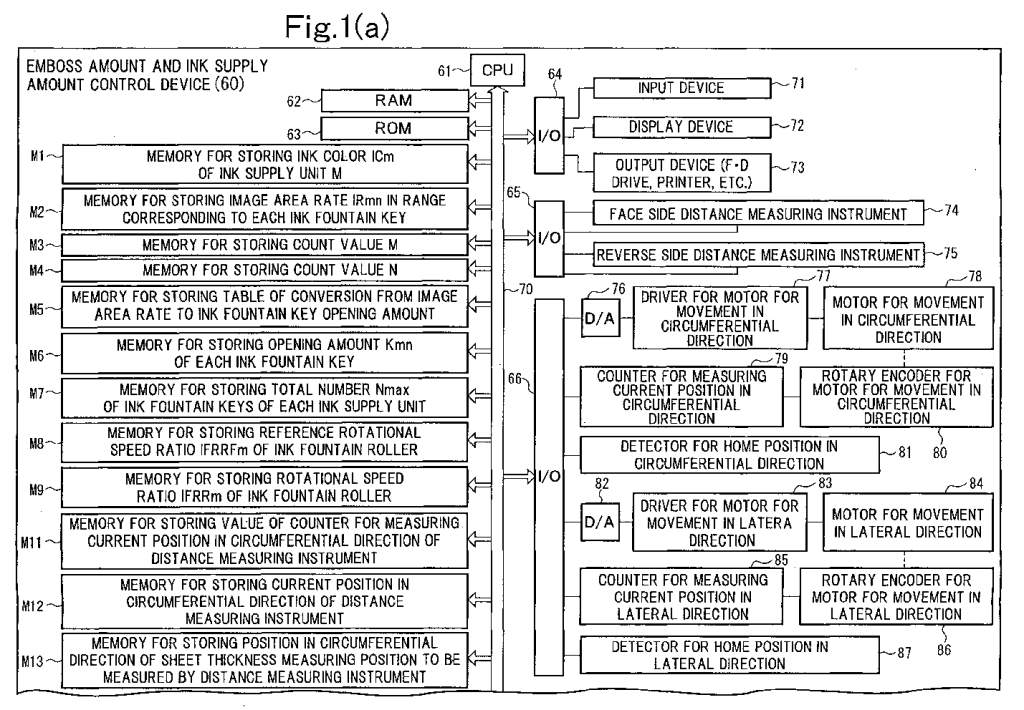
Welcome to our article on printing ink quality control! In today’s fast-paced printing industry, ensuring the highest standards of ink quality is paramount for achieving exceptional print results. Whether youβre a printing professional or someone with a keen interest in the field, understanding the importance of quality control in printing ink is crucial.
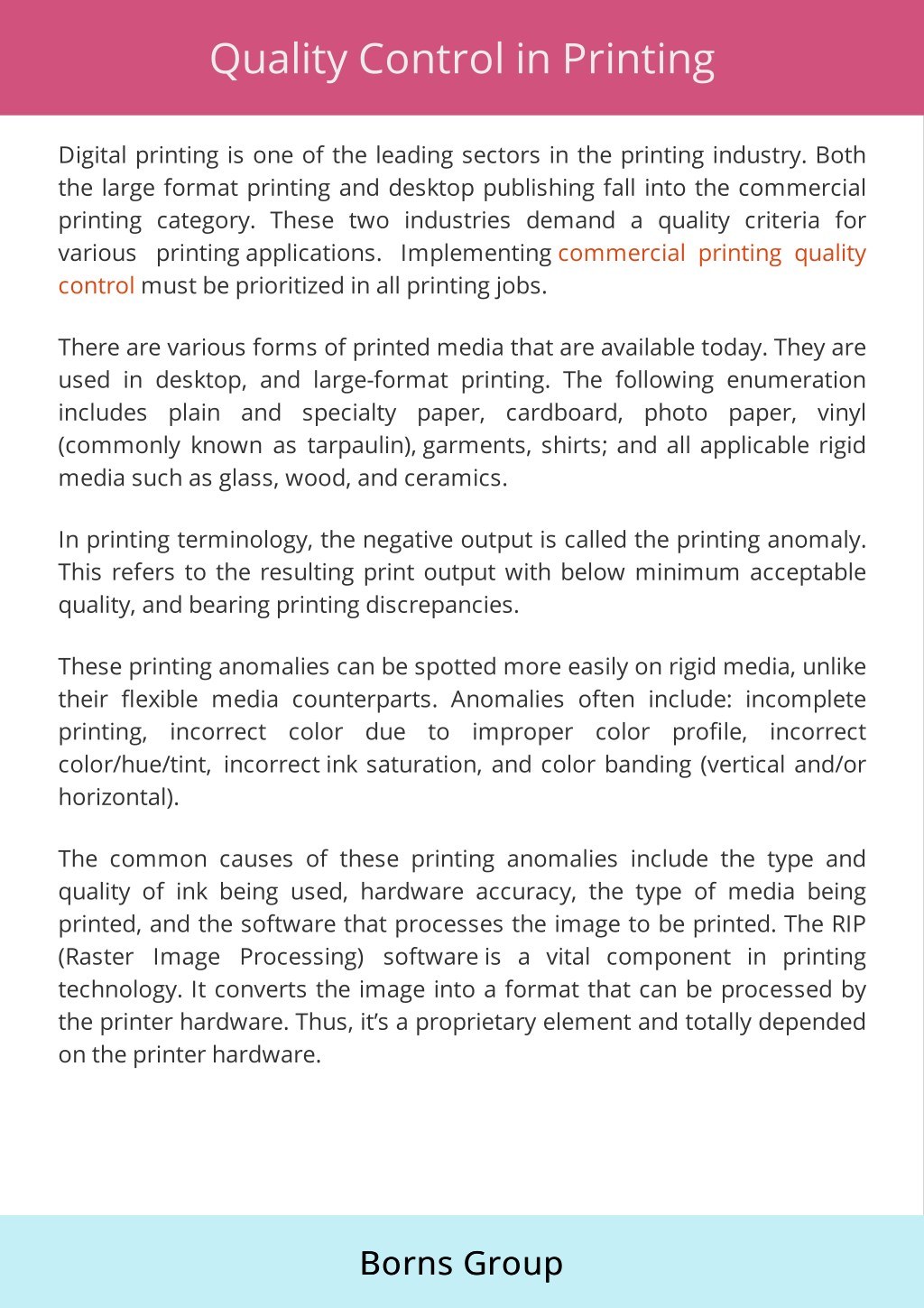
Image Source: slideserve.com
In this article, we will delve into the intricacies of printing ink quality control and its significance in achieving outstanding print outcomes. We will explore the different aspects of quality control, including its definition, the individuals involved, the timeline, the location, the reasons behind its implementation, and the methods employed. So, let’s dive right in!
What is Printing Ink Quality Control? π¨οΈ
Printing ink quality control refers to the systematic process of monitoring and managing the various factors that influence the quality of ink used in the printing process. It involves a comprehensive assessment of ink characteristics such as color accuracy, viscosity, drying time, adhesion, and overall performance.
This quality control process ensures that the ink meets the desired specifications and conforms to industry standards. By implementing quality control measures, printing companies can enhance their print quality, reduce waste, and improve overall customer satisfaction.
Who is Involved in Printing Ink Quality Control? π§βπ¬
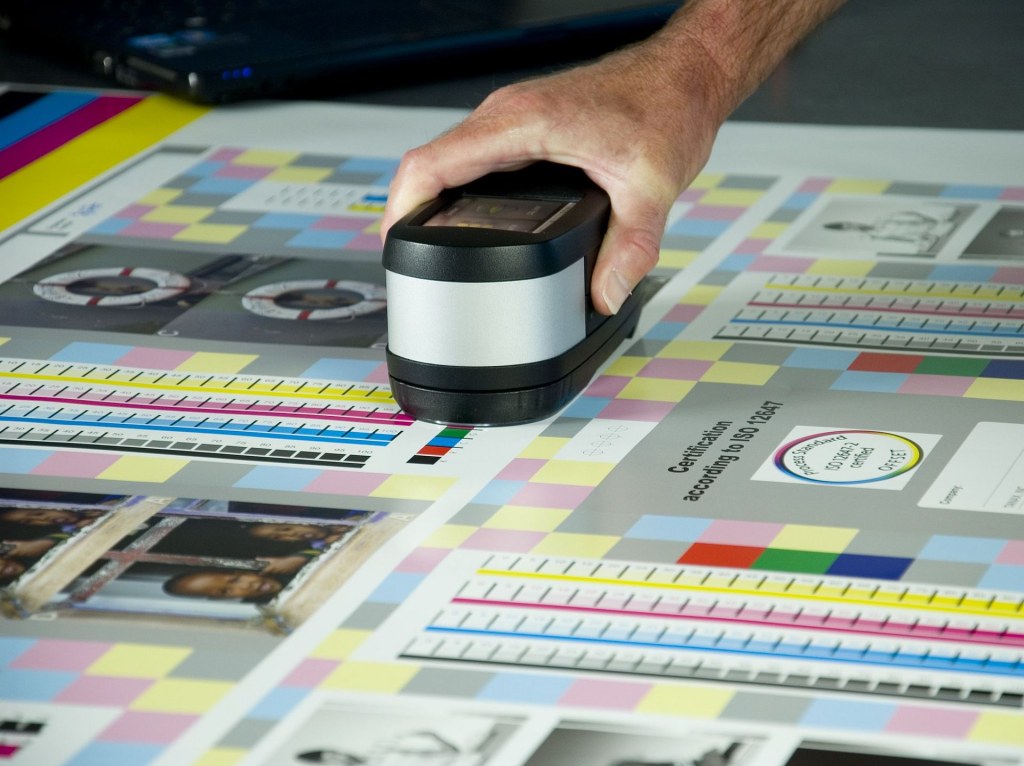
Image Source: fogra.org
Printing ink quality control requires a collaborative effort from different stakeholders. This includes ink manufacturers, printing press operators, quality control technicians, and print production managers. Each individual plays a vital role in ensuring that the ink used meets the required quality standards.
Ink manufacturers are responsible for producing high-quality ink formulations that meet industry standards. Printing press operators work closely with the ink, ensuring proper handling, storage, and usage. Quality control technicians perform regular tests and inspections to ensure the ink’s quality, while print production managers oversee the entire process to maintain consistency.
When does Printing Ink Quality Control Occur? β°
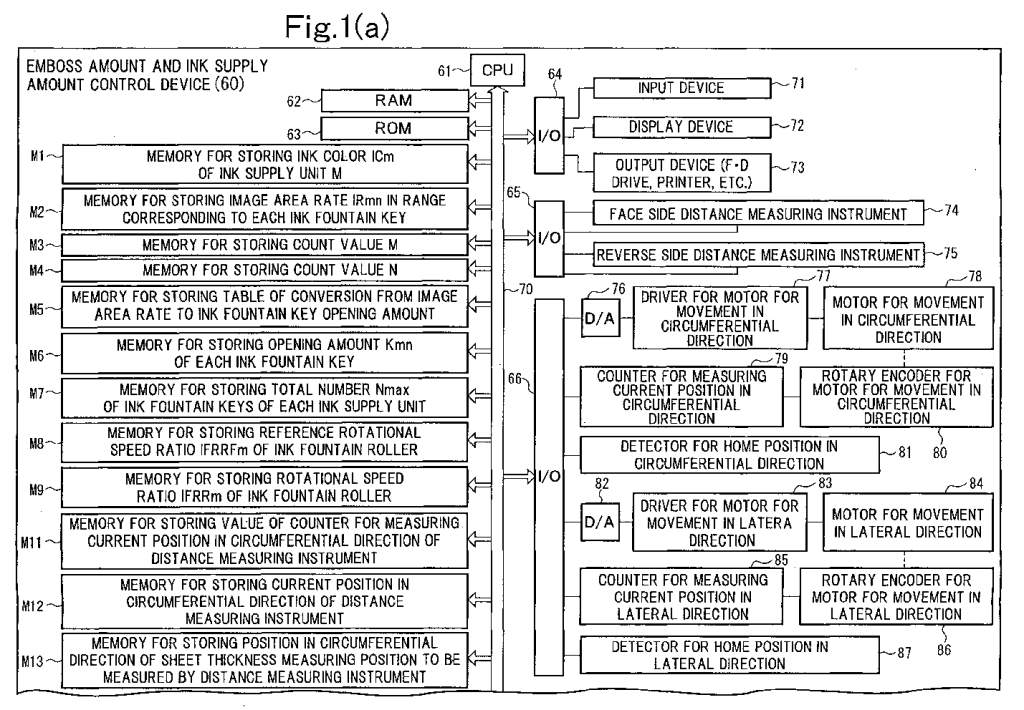
Image Source: googleapis.com
Printing ink quality control is an ongoing process that occurs at various stages of the printing workflow. From the initial production of the ink to its usage during printing, quality control measures are implemented at every step.
Prior to the ink being dispatched to the printing facility, manufacturers conduct rigorous quality checks to ensure the ink’s suitability for use. Once the ink reaches the printing press, operators perform regular checks to ensure its consistency and performance. Additionally, quality control tests are conducted during and after printing to assess the final print quality.
Where is Printing Ink Quality Control Implemented? π
Printing ink quality control is implemented both at the ink manufacturing facilities and the printing press. At the manufacturing stage, quality control laboratories are equipped with advanced equipment to analyze the ink’s properties and determine its conformity to specifications.
Within printing facilities, dedicated quality control areas are established to monitor ink performance. These areas house specialized testing equipment, such as spectrophotometers and viscosity meters, to assess ink quality. Adherence to environmental conditions, including temperature and humidity, is also crucial to ensure consistent ink performance.
Why is Printing Ink Quality Control Important? β
The implementation of printing ink quality control is essential for several reasons:
1. Consistency: Quality control measures ensure consistent ink performance, leading to uniform print quality throughout the print run.
2. Cost Reduction: By detecting and rectifying ink quality issues promptly, wastage is minimized, resulting in cost savings.
3. Customer Satisfaction: High-quality ink leads to superior print results, exceeding customer expectations and enhancing satisfaction.
4. Brand Reputation: Printing companies that consistently deliver exceptional print quality gain a strong reputation in the market, attracting more clients.
5. Compliance: Adhering to industry standards and regulations is crucial for maintaining legal compliance and meeting client requirements.
How is Printing Ink Quality Control Implemented? π οΈ
Printing ink quality control is implemented through various methods and processes:
1. Ink Testing: Regular testing is conducted to assess ink properties such as color accuracy, viscosity, pH levels, and adhesion.
2. Statistical Process Control: Statistical tools are used to monitor ink quality over time, identifying trends and patterns that may indicate potential issues.
3. Training and Education: Continuous training programs are provided to ink manufacturers, printing press operators, and quality control technicians to enhance their knowledge and skills.
4. Documentation: Detailed records are maintained to track ink batches, test results, and any corrective actions taken.
5. Calibration: Testing equipment is regularly calibrated to ensure accurate and reliable results.
Advantages and Disadvantages of Printing Ink Quality Control
Advantages:
1. Enhanced Print Quality: Quality control measures result in superior print outcomes, meeting and exceeding client expectations.
2. Cost Savings: By minimizing ink wastage and rework, printing companies can reduce production costs.
3. Improved Efficiency: Streamlining ink quality control processes leads to smoother production workflows and increased efficiency.
Disadvantages:
1. Time-Consuming: Implementing thorough ink quality control measures may require additional time and resources.
2. Increased Costs: Setting up quality control laboratories and investing in testing equipment can be a significant investment.
3. Complexity: The technical nature of ink quality control may pose challenges for individuals without proper training and expertise.
Frequently Asked Questions (FAQ)
1. Is ink quality control only relevant for offset printing?
No, ink quality control is important for all printing processes, including offset, flexography, gravure, and digital printing.
2. How often should ink quality control tests be conducted?
The frequency of tests depends on several factors, including the type of ink, print volume, and customer requirements. However, regular daily or weekly testing is common in most printing facilities.
3. Can ink quality control prevent color variations in print?
While ink quality control significantly reduces color variations, other factors such as substrate quality and press settings also influence print color accuracy.
4. Can ink quality control detect contamination issues?
Yes, ink quality control tests can identify contamination issues such as foreign particles or impurities in the ink.
5. How can I ensure ink quality control compliance?
Adhering to industry standards, conducting regular tests, and implementing proper training and documentation protocols are key to ensuring ink quality control compliance.
Conclusion
In conclusion, printing ink quality control plays a vital role in achieving exceptional print results. By implementing robust quality control measures, printing companies can enhance print quality, reduce costs, and improve customer satisfaction. It is crucial for ink manufacturers, printing press operators, and quality control technicians to collaborate effectively to ensure the highest standards of ink quality throughout the printing process.
Final Remarks
Dear Readers,
Thank you for joining us on this informative journey through the world of printing ink quality control. We hope this article has shed light on the significance of quality control in achieving outstanding print outcomes. As you continue your printing endeavors, remember to prioritize ink quality control to ensure excellence in every print you produce.
Wishing you success and excellence in all your printing endeavors!
This post topic: Printer Ink